Prep your work for 3D printing: 8 top tips
Get the most out of your 3D models when prepping for print, and avoid costly mistakes.
3D printing has become hugely popular. If you want to start printing your own 3D art, there are a few things to look out for to get the best results. Here I will show you how to make the most of your models and avoid disappointing or disastrous results. Follow these tips and your prints should be easy to manage and look great.
01. Work to scale
Working to scale is important. Although most 3D printers come with software that can adjust scale, transforms and rotations (mostly to help the design fit on the build platform better) it’s best practice to work at scale in 3D, no matter what your delivery method is. It makes collaboration easier as well as ensuring your assets will work across projects.
02. Seal up any holes
Beware of non-manifold meshes. For a model to print successfully it needs to be water-tight, so make sure there are no holes in the surface. Most apps have a tool for closing holes automatically, or alternatively you can use a bridge tool. If you want your print to be hollow you need to model it as such, giving it a wall thickness. Sometimes an easy way to do this is simply to extrude all your polygons inwards.
03. Tackle overlapping pieces
Separate meshes will be printed as such, but if this is undesirable you can get around it by making sure your pieces intersect. The hinged arm joint in this character needs to print as one solid piece, so the hinge has been very slightly enlarged to ensure the export sees the overlap and prints a single part. Of course, printing different parts of your model separately means you can test out different poses before gluing your character together.
04. Convert to triangles
Convert everything to polygons, and preferably triangles. Most 3D printers need a specific file type to print a mesh successfully and, while some software has exporters for these files, it’s best to take control of this part of the process yourself. If you use things like sweeps or lofts, convert them to polygons before you save for printing. This way you control what happens, how many polygons are created and how smooth the results are. If you can convert to triangles even better, as you will see the printable results in your viewport.
05. Plan for support structures
Most prints will need some form of support structure in order to print properly, providing a base to build on and supporting any overhanging parts. This structure needs to be trimmed off and cleaned after the print, so think about where it should sit. Some print software will help you with this.
Think about how you pose your model to make clean-up easier. For example, lying this robot on his back means the supports will be available for all areas that need it (like the arms and neck) and clean-up will be required only in areas that are seen less.
Get the Creative Bloq Newsletter
Daily design news, reviews, how-tos and more, as picked by the editors.
06. Consider orientation
Orientation can be a very important aspect of 3D printing. Many printers can print fine detail but often you can still see the line where the different layers of material have been extruded. You can counter this by orienting your mesh in way that minimises how visible the lines will be. Printing a head from top to bottom will highlight the lines, but if you print at 40-50 degrees they will be less noticeable. In other cases, like this pot, the lines are better off being horizontal.
07. Avoid unnecessary detail
Be aware of the printer's limitations. These two prints are of the same mesh, from the same printer, but at different scales. If you know how large your print will be up-front, you can model the appropriate level of detail. The larger print shows surface texture like the shaved head – but if you aren’t printing that size you don’t need to bother modelling it. It will just slow the modelling and the printing down.
08. Use suitable glue
The best tip for printing in 3D is to use a suitable glue to help your filament stick to the build platform. Pritt Stick or any similar type of soft paper glue is perfect as it is easy to apply, just strong enough to hold the extrusion in place and not so tough that you risk breaking the print when trying to remove it. The second part of this tip is to purchase a thin wallpaper scraper. Use this to remove the print from the build platform and it should take the glue with it.
Related articles:
Thank you for reading 5 articles this month* Join now for unlimited access
Enjoy your first month for just £1 / $1 / €1
*Read 5 free articles per month without a subscription
Join now for unlimited access
Try first month for just £1 / $1 / €1
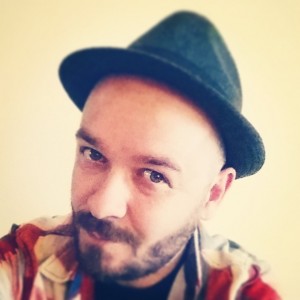
Rob Redman is the editor of ImagineFX magazines and former editor of 3D World magazine. Rob has a background in animation, visual effects, and photography.