Why 3D printing is the future of design
It's time to get on board with 3D printing, as it moves from hobby to the mainstream.
It is said that most any prediction will come true if we wait long enough. Steve Jobs was credited with being uniquely prophetic in his lifetime (though he played a hand in making his prophecies come true, so is that prophecy, or good marketing?).
Either way, Jobs predicted that every computer user would have a page printer by its side, which has mostly come true. He also predicted the day when every computer would have a 3D printer by its side. This prophecy has yet to come true, but is far less sci-fi now than when he first said it in the early 1990s.
Ask the average person on the street what 3D printing is, and you are still likely to get a blank stare. This is hardly common stuff yet. But it's beginning to feel like the day of this technology breaking through to the consumer is coming soon. And there are plenty of forces working very hard to make this happen.
Origins
In industry, 3D printers have been around in various forms for decades. Chuck Hull of 3D Systems Corp is credited with creating the first commercial unit in 1984. Uses for the machines have traditionally been in the rapid prototyping arena. This is ideal for quickly seeing if a product or part of a product will work, fit, and generally do the job intended.
For some, the wholly grail of 3D printing was to move it from this more limited pre-production niche into the more significant role of actual production, of an either limited or short run variety. This has already become the reality in another field, where short run digital printing presses were used to create the now mainstream print-on-demand (POD) books found on Amazon and B&N stores.
The idea is simple. Why do a whole production run for an item that will have small numbers of orders, when POD fills the need nicely?
Endless possibilities
For the smaller-scale 3D professional and designer, and even the advanced amateur, the applications of 3D printer are almost endless. A design shop could output a client's logo for display in the offices, or create quick mock ups to present to the client in more elaborate pitches. In the home setting, small parts for the coffee maker or vacuum could be quickly fabricated, rather than having to wait days for delivery from the OEM.
Get the Creative Bloq Newsletter
Daily design news, reviews, how-tos and more, as picked by the editors.
In fact, we will likely see the day when parts are simply available as meshees online, ready to be downloaded and printed locally. In a sense, this is like having a Star Trek transporter right on your desk. For objects, if not people.
Additive v subtractive
Besides the more obvious variations of larger and smaller units, the significant options are additive or subtractive technologies. In other words, to create your item, does the printer start with a large block of some material, and whittle away (drill away actually) at it until it is in the right shape, a la Michelangelo and his David statue? Or instead, does it use raw materials - usually a plastic of some sort threaded on a supply roll - to add dot by dot until it build up?
Each technology has its pros and cons. Additive allows for more detail in the negative spaces, whereas working subtractively opens the door to working with other materials like metals, glass, etc.
In either case, a printer's output resolution can vary as well, much like that of page printers, but in three dimensions instead of two. And like page printers, 3d printer resolution tends to be in the 250-300 dpi range for most, and upwards of 1600 dpi on higher end units. So output smoothness will vary, but we can expect that to improve in the coming years.
Finally, but importantly, many 3D printers will not only create the shape, but also offer the option to either apply or actually include any texture map colorings that have been applied to the model in the software. The results can be impressive.
A perfect storm
So what are the forces that are bringing 3D printing to the fore? There are quite a few really. The technology has been evolving for over three decades now, and is both reliable, and more recently also affordable. On the customer's side, there are far more folks, both professionals and amateurs, using 3D software today, thus making these tools accessible and creating a demand for outputting cyber-creations.
And major companies are opening up to respond to this burgeoning desire. For example, right here in New York City, our previous Mayor Bloomberg was an avid technologist who did much to foster new high-tech growth. This included putting his weight behind the upstart 3D printing industry, and companies like Shapeways, a company that acts much like the old Linotype output service bureaus of years ago. The difference, of course, is that they output your 3D model files instead of high resolution pages.
Though NYC is certainly a great hub for all things digital and a sweet-spot for 3D printing's future, such service bureaus have been popping up all over the world over recent years. And since all offer mailing services, location is not as critical when time is not of the essence. A list of many of the larger services can be seen here.
Personal 3D printers
Being able to send things out to a service is always nice. But there are some of us, this author included, that prefers to roll their own, in their own shop. To this end there is a new fiercely competitive market of personal 3D printers to choose from. Companies like Makerbot have been the most commercially successful, but there are dozens of companies, large and small, in the personal 3D printer game. Many are sold as assembled units, others as kits (an evolving list can be seen here).
Prices for units like these have dropped dramatically in the last few years from the many thousands of dollars (US), or even tens of thousands of commercial units, to just a couple of thousand dollars, or even less. For example, the crowd funded MakiBox sold its kit for just $350.
Photoshop enters the fray
It's not like Adobe has been out of the loop the last few years. To the contrary, we have seen them systematically adding more and more 3D functions to Photoshop since its CS3 Extended incarnation began this march forward. Now in Photoshop CC (which is really Photoshop version 14, with the 'Extended' moniker cast aside), Adobe has stepped up to add additional 3D printing controls.
While Photoshop could print to a 3D printer before, this version adds a host of features and functionality that make the process much easier for the creatives that are not expert in the 3D printing process. This probably includes most of us, even those of us that have done 3D work for years.
Adobe's aim is to make Photoshop the Swiss army knife of all things graphic, including 3D printing. To this end they have worked to make the end-to-end process smoother by having the program find and fix a range of geometry construction issues that presumably would be beyond the capabilities of the average user. (And perhaps beyond the user toolset in the program as well.) They are shooting for the 'it just works' award, and we all support that goal.
When at the point you are ready to print your model, Photoshop allows either the selection of a locally attached printer, or that of automatically prepping for output to a service. Adobe has a strategic alliance with Shapways.com, which is given as a dropdown menu option for prepping that model. Then when you go to the 3D>3D Print... you are given both a preview of the final geometry, as well as an estimate of output cost from that vendor. Presumably other vendors will be able to be added to this drop down offering.
For all its additions, Photoshop is still not a 3D modeler. Many meshes will need to be imported. But there is still an ever-increasing list of shapes you can create just within PS, and it's worth the effort to play with these tools a bit and figure out what it can do for you and your clients.
3D printing on show
You can always tell when a topic is the next hot new thing by the fact there will be conventions or expos produced to entertain, inform and sell to those throngs of folks who are into this new thing. Well sure enough, there has been a 3D PrintShow event that has been touring around this year. They ran shows all over the world including London, Paris, Brazil, New York, and others. In addition to an entire floor of vendors selling all things 3D print and associated 3D, there was an additional art gallery floor of 3D printed art. There were lectures, demonstrations and parties.
All of this is still somewhat new. But while clients may not be pestering you for such services this year or next, it's a great time to expose yourself to some of these new capabilities. After all, you probably already have Photoshop CC sitting there waiting to be tried out.
Words: Lance Evans
Lance Evans is creative director of Graphlink Media. He has written books on 3D, and produced the 3DNY Seminars for Apple and Alias.
Thank you for reading 5 articles this month* Join now for unlimited access
Enjoy your first month for just £1 / $1 / €1
*Read 5 free articles per month without a subscription
Join now for unlimited access
Try first month for just £1 / $1 / €1
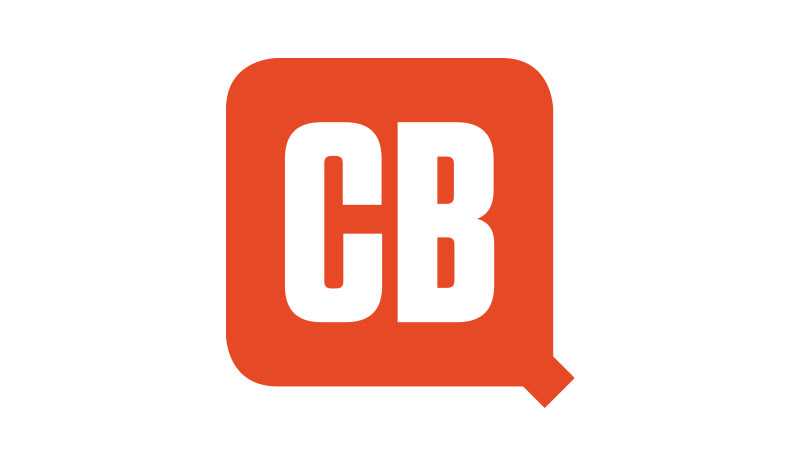
The Creative Bloq team is made up of a group of art and design enthusiasts, and has changed and evolved since Creative Bloq began back in 2012. The current website team consists of eight full-time members of staff: Editor Georgia Coggan, Deputy Editor Rosie Hilder, Ecommerce Editor Beren Neale, Senior News Editor Daniel Piper, Editor, Digital Art and 3D Ian Dean, Tech Reviews Editor Erlingur Einarsson, Ecommerce Writer Beth Nicholls and Staff Writer Natalie Fear, as well as a roster of freelancers from around the world. The ImagineFX magazine team also pitch in, ensuring that content from leading digital art publication ImagineFX is represented on Creative Bloq.